Production Processes
BADIKAN TRANSFORMER produces distribution transformers in accordance with TS, IEC, ANSI and BS standards, in the power range between 25KVA-2500 KVA and voltage levels up to 6.3-11-20-36 kV, in either HERMETIC type, which are fully enclosed to atmosphere, or EXPANSION TANK type, which are open to atmosphere, based on customer demands and the required country voltage levels.
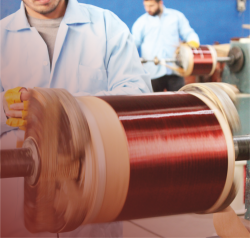
Winding
Cover insulation is provided by improved rosin paper ( DPP ) thermally for low voltage winding conductor copper plate windings...
Distribution Transformer Windings:
The low voltage winding conductor is made of copper sheet in strip windings and the layer insulation is provided with thermally improved resin-impregnated paper (DPP).
The high voltage winding conductor is made of round copper wire coated with enamel, and the insulation is paper-coated flat copper wire. The layer windings are wrapped with computer-controlled fully automatic machines, and the layer insulation is formed in the shape of strip-shaped electrical insulation papers (electric Kraft, thermally improved Kraft and resin-impregnated thermal paper). The layer insulation structure created in this way not only increases the resistance of the winding to overvoltage shocks, but also enables the production of seamless, solid, and perfectly-featured coils.
Distribution Transformer Windings:
The low voltage and high voltage winding conductor is copper. Depending on the transformer power, the windings are wound by using copper wire covered with insulating paper as floor winding, continuous disc winding, helical winding or screw winding.
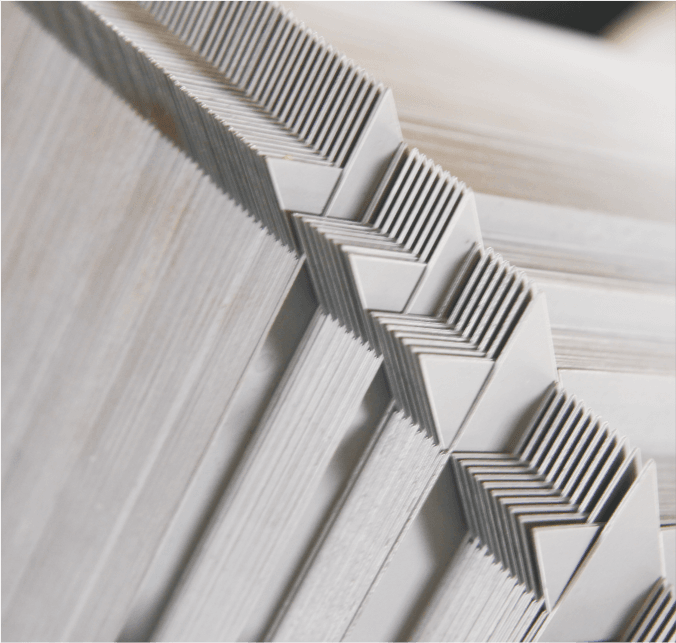
Magnetic Circuit
It is cored type and manufactured of M5, M4 and M3 silicon alloyed sheets with thicknesses 0.30, 0.25 and 0.23 mm of which crystals are directed.
All the sheets used in the magnetic circuit are cut in the CNC controlled cutting machine, stacked and lined up to form a magnetic circuit.
Magnetic circuit cutting and arrangement is done by a method called step-lab which minimizes iron losses. The core is lined up with diagonal and longitudinal step-lab applications.
.
Noise levels are minimized by tightening the core sheets with U profile and steel studs passing through the yoke insulated pipes.
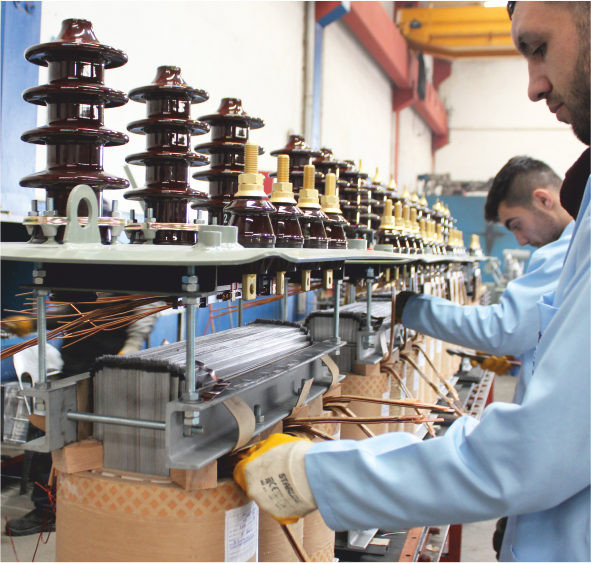
Active Part
For transformers of which core and coils are ready, coils are mounted by tightening on the core and against each other by means of bars
At the same time, the coils are equipped with a protection system against axial forces. The setting terminals leading to the commutator or step switch are prepared for the active part by making the necessary connections and welding with silver electrodes.
Active parts are dried in ovens using an air circulation method to remove any moisture present in the solid insulation materials, according to a program that depends on the power and voltage of the transformer.
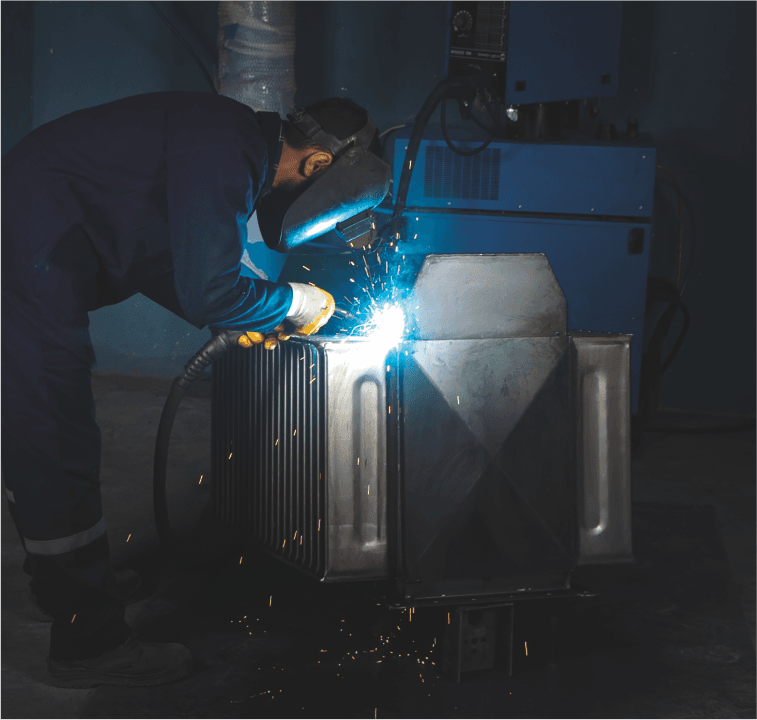
The Transformer Tank
It is used for preservation of cooling and insulation material in oil-immersed type transformers. Transformers up to 3150 KVA are wave-walled, depending on cooling surfaces, and those with larger powers are manufactured as radiator boilers.
In boiler manufacturing, a CNC controlled plasma machine is used. Boilers that have finished assembly and welding works are subjected to a leak tightness test under pressure according to IEC standards. The vacuum resistance of wave wall boilers is designed to be 0.65 bar, and that of radiator boilers is 1 bar. Boilers that are manufactured according to customer demand are subjected to sandblasting. The boiler cover is designed for the removal of the suture tips.
There are insulators, phase marking, lifting ears for lifting the active part, thermometer pocket, grounding bush and additional equipment on the cover.
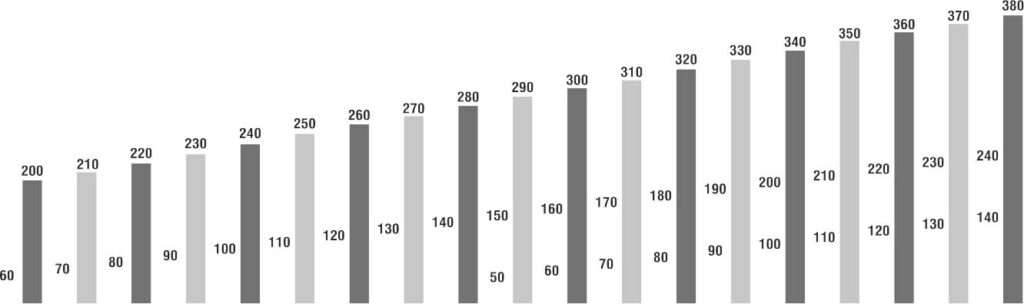
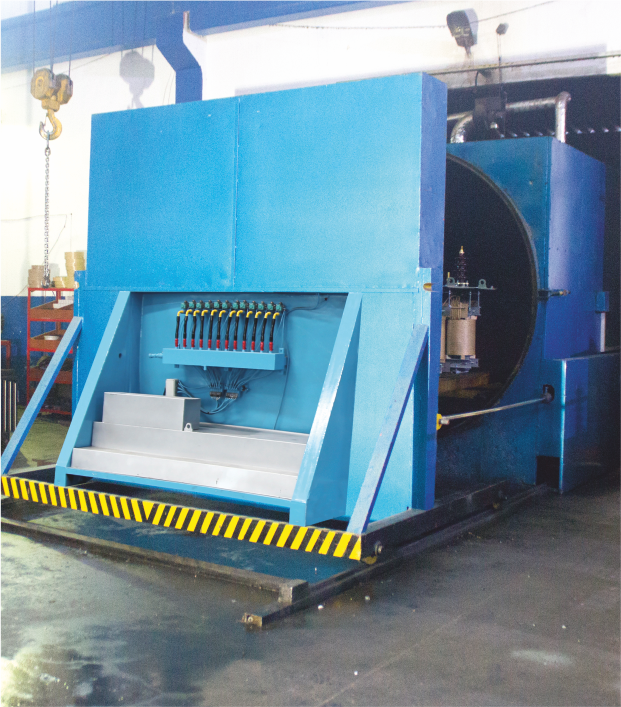
DRYING AND OIL FILLING
After the active part assembly of the transformers is finished, they are placed in the tank and oil is filled in a vacuum chamber, after drying at a temperature of 120 degrees in drying ovens.
The air remaining in the transformer's boiler in the vacuum chamber is sucked in and the insulating oil is fully penetrated into the active part. The filled oil provides insulation and cooling.
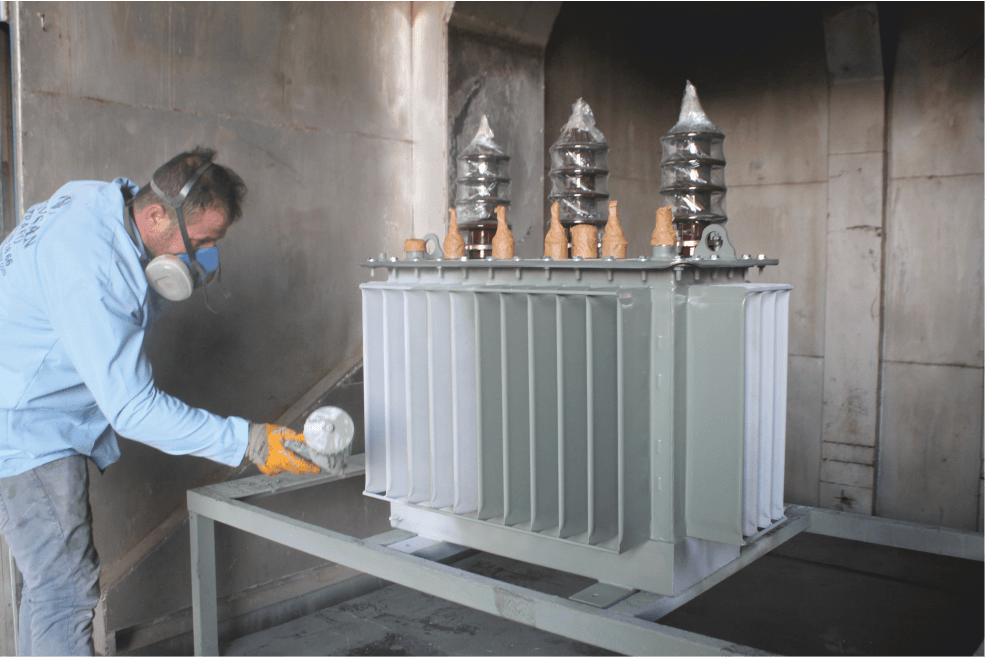
Painting
The completed boilers are painted by spray method. Standard painting consists of one primer and two top coats. The total film thickness is not less than 105 microns.
The standard transformer color is RAL7033, called cement gray.
Depending on the customer's request, it is possible to paint in different structures (such as zinc coating), different thicknesses and different color codes.
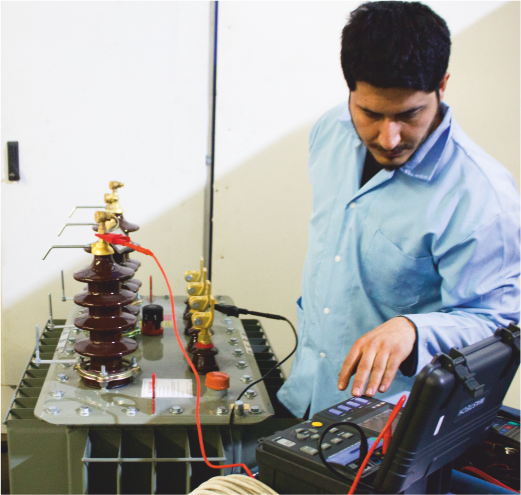
Tests
Routine Tests
- Measuring winding resistances
- Measuring conversion rates
- Checking the polarity or connection group
- Measurement of short-circuit voltage and load losses
- Measurement of no-load losses and current
- Induced voltage test
- Applied voltage test
- Measuring insulation resistances
- Measurement of DC Insulation resistance
Type Tests
- Temperature increase (Warm-up Test)
- Full wave impact test
- Measuring the audible noise level
- Boiler life test (For Hermetic Transformers)
*Except for the mechanical strength test against short circuits, all other type tests are carried out in our company's laboratory.
Special Tests
- Checking the breakdown voltage of oil
- Measuring paint thickness
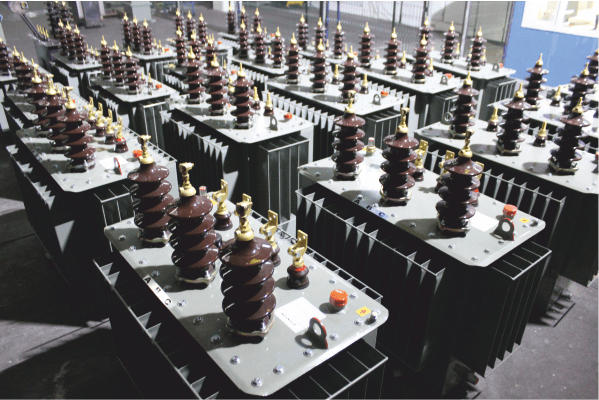
Connection Methods
In distribution transformers up to 1600 kVA, the Dyn 11 (TRIANGLE/YILDIZ neutral removed) connection type standardized by TEDAŞ is applied, other connection types can be used if desired.
For networks with high unbalanced loads in phases, transformers up to 200 kVA can also be connected as Yzn 11 (STAR/ZICZAK - neutral removed) if desired. In transformers larger than 1600 kVA, the connection type requested by the customer is applied.